A serious potential failure mode of commercial fusion scale tokamaks will be the creation of relativistic “runaway” electrons that are created when electrons are accelerated by an inductive loop voltage faster than they are slowed by collisions during a plasma disruption. These high energy electrons can end up carrying multi-MA of current. The runaway electron mitigation coil (REMC) seeks to prevent the build-up of a significant runaway electron population by using perturbed magnetic fields to significantly reduce the confinement time of the electrons. Essentially, the electrons will be lost from the plasma before they are accelerated to quantities and energies that can damage the plasma facing components. The asymmetric nature of the coil provides a perturbing field that leads to stochastic flux surfaces when 100s kA of current is passed through the coil. The coil itself is passively driven: the current in the coil is generated by inductively coupling to the plasma as it undergoes a current quench and loss of magnetic energy.
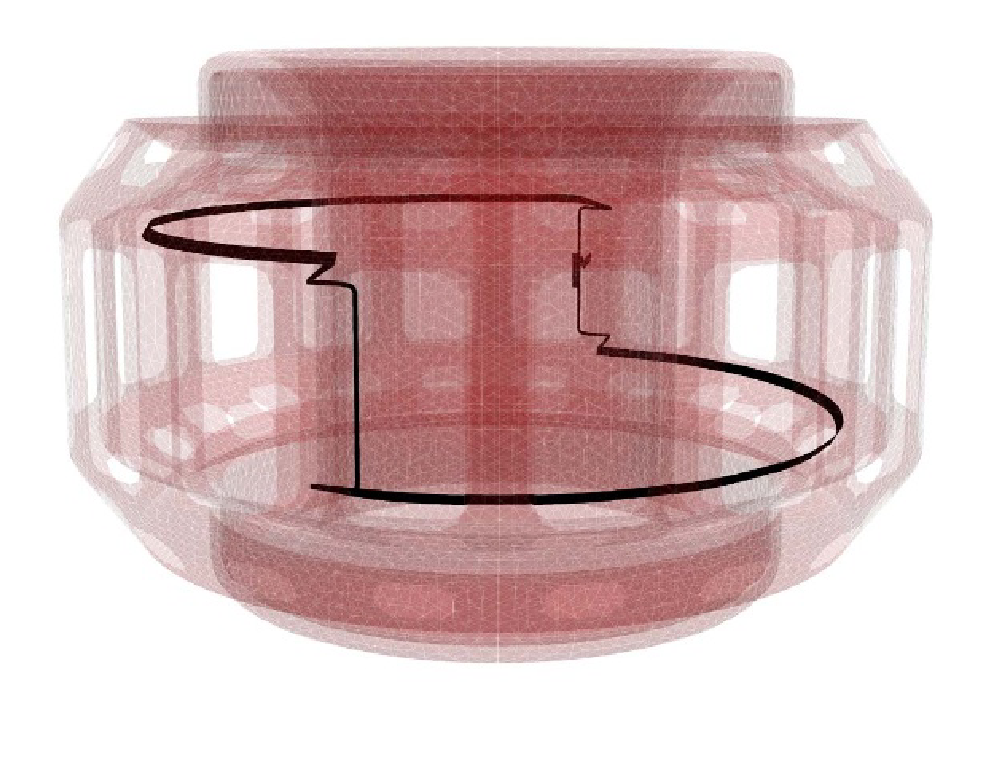
This project focuses on the implementation challenges of placing a plasma-facing, high-voltage, high-current coil in a high (8 T) magnetic field, high neutron fluence machine like SPARC. One such challenge is ensuring proper electrical insulation of the coil from the surrounding support structure and vacuum vessel. Spray coated alumina was identified as the insulation material most likely to provide the necessary voltage stand-off while also surviving the unique in-vessel environment of SPARC. Test samples of the alumina are being created and tested in three phases, with each phase being more representative of the true geometry of the REMC design. The electrical breakdown and mechanical loading test results will be used to iterate on the REMC design to ensure it can operate effectively for Q>1 plasma discharges in SPARC.
This project also provides scoping and assessment of the ex-vessel switch and busbar hardware shown in the figure above. This includes effects of the ex-vessel hardware on REMC circuit performance, neutron irradiation testing of potential switch hardware, and scoping the use cases of the REMC in a disrupting plasma given the switch performance.
The REMC hardware testing team is led by Postdoc John Boguski with close collaboration with Ryan Sweeney (CFS) and Alex Tinguely. John Boguski’s supervisor is Alex Tinguely.